Molding Precision: Elevating Standards in Metal Fabrication
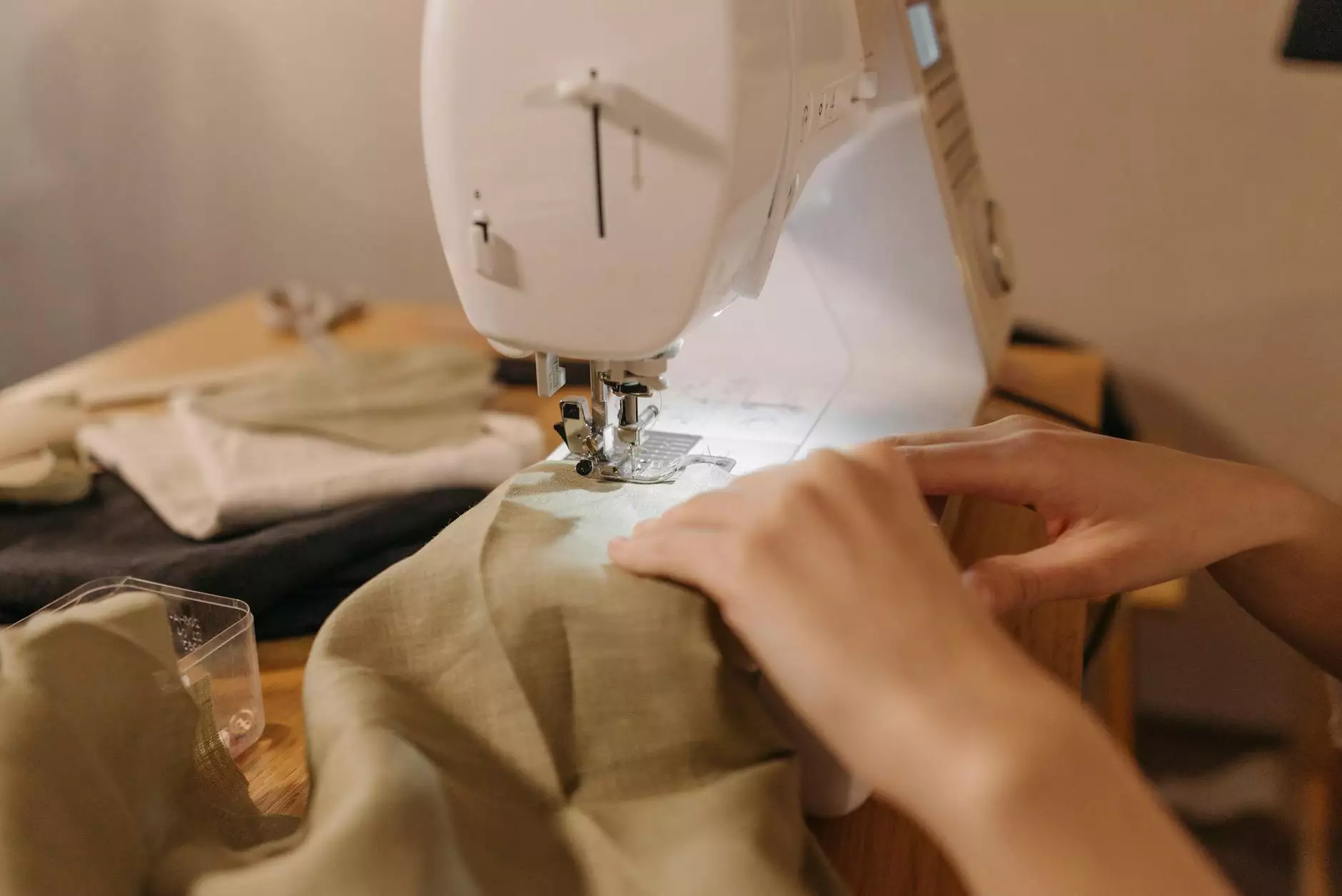
Molding precision is not just a buzzword in the metal fabrication industry; it is a critical element that defines the quality and efficiency of the manufacturing process. At DeepMould, we consider ourselves leaders in this domain, honing our skills and technologies to ensure that every part we create meets the highest industry standards.
Understanding Molding Precision
The term molding precision refers to the accuracy and exactitude achieved during the manufacturing process of metal components. This precision is vital for several reasons:
- Quality Assurance: Consistent precision leads to high-quality finished products that meet or exceed customer expectations.
- Interchangeability: High precision enables parts to be interchangeable, facilitating repairs and replacements.
- Cost Efficiency: Precise molds reduce material waste, leading to cost savings in production.
The Importance of High Precision in Metal Fabrication
In the world of metal fabrication, the demand for high precision is growing tremendously. Industries such as automotive, aerospace, and electronics require components that not only function perfectly but can also withstand rigorous conditions. Here are several reasons why molding precision is critical:
- Safety: In industries like aerospace and automotive, even a minor deviation in precision can lead to catastrophic failures. Ensuring rigorous precision standards enhances safety.
- Performance: Precision in parts guarantees optimized performance, allowing machinery and vehicles to operate at peak efficiency.
- Regulatory Compliance: Many industries are governed by strict regulatory standards that demand high-quality and precise components.
Our Approach to Molding Precision at DeepMould
At DeepMould, we have developed a comprehensive approach to achieve and maintain molding precision throughout our manufacturing processes. This approach involves several key components:
1. Advanced Technology
We invest heavily in the latest technologies, including:
- Computer Numerical Control (CNC): CNC machines provide unparalleled precision by controlling the factory tools using coded instructions.
- 3D Printing: This technology allows for rapid prototyping and exceptionally detailed designs.
- Laser Cutting: The use of lasers for cutting metals reduces the chance of human error, enhancing precision.
2. Skilled Workforce
A proficient team is essential in maintaining high standards of molding precision. Our workforce is trained to adhere to best practices and is continuously educated on emerging technologies and methodologies.
3. Rigorous Quality Control
Quality control is at the heart of our operations. Every part undergoes a strict evaluation process that checks for dimensional accuracy, surface finish, and overall integrity. Our quality assurance team employs:
- Dimensional Inspection: Using advanced measuring tools to ensure that every dimension meets specified tolerances.
- Non-Destructive Testing: Techniques like ultrasonic and magnetic particle inspections that ensure integrity without damaging the part.
Applications of Molding Precision in Various Industries
Metal fabrication that emphasizes molding precision finds applications across numerous sectors. Here’s how different industries leverage high precision:
Aerospace Industry
The aerospace industry demands the highest standards of safety and performance. Components such as brackets, frames, and joints require precise specifications to ensure the structural integrity of the aircraft. Any discrepancies can lead to significant safety risks.
Automotive Sector
In automotive manufacturing, parts like engine blocks, chassis components, and transmission parts need to fit together flawlessly. Precision molding ensures that all components work seamlessly, enhancing the performance and reliability of vehicles.
Electronics Manufacturing
With the rise of smart devices, the electronics industry has experienced an increased demand for tiny, precise components. From circuit boards to casing, every part must meet strict precision standards to ensure functionality.
Innovations in Molding Precision
The landscape of molding precision is constantly evolving. Here are several recent innovations that have revolutionized metal fabrication:
- Smart Manufacturing: The integration of IoT (Internet of Things) devices in manufacturing processes helps monitor efficiency and precision in real-time.
- Adaptive Tooling: Tools that can adjust their parameters during operation to improve precision based on feedback data.
- Eco-Friendly Practices: Innovations in eco-friendly materials not only enhance precision but also reduce environmental impact.
The Future of Molding Precision
As industries continue to advance, the demand for molding precision will only increase. With the ongoing development of technologies like AI and machine learning, we are entering an era where manufacturing processes will become even more automated and precise. The future will likely see:
- Greater Customization: Enhanced capabilities for custom parts that precisely meet unique customer specifications.
- Improved Speed and Efficiency: Fast-paced production techniques that still maintain high standards of quality and precision.
- Widespread Adoption of Additive Manufacturing: Techniques like 3D printing becoming the norm for producing precise components more efficiently.
Conclusion
In the competitive field of metal fabrication, molding precision stands out as a key differentiator. At DeepMould, we pride ourselves on our commitment to precision and quality, leveraging advanced technology and a skilled workforce to produce superior metal components for various industries. As we look ahead, we remain dedicated to innovation and excellence, continuously improving our processes to meet the evolving needs of our customers. Trust DeepMould for your precision molding needs, and experience the difference in quality that precision brings.
For more information on our services and how we can help your business achieve its goals through top-quality metal fabrication, visit our website at deepmould.net.